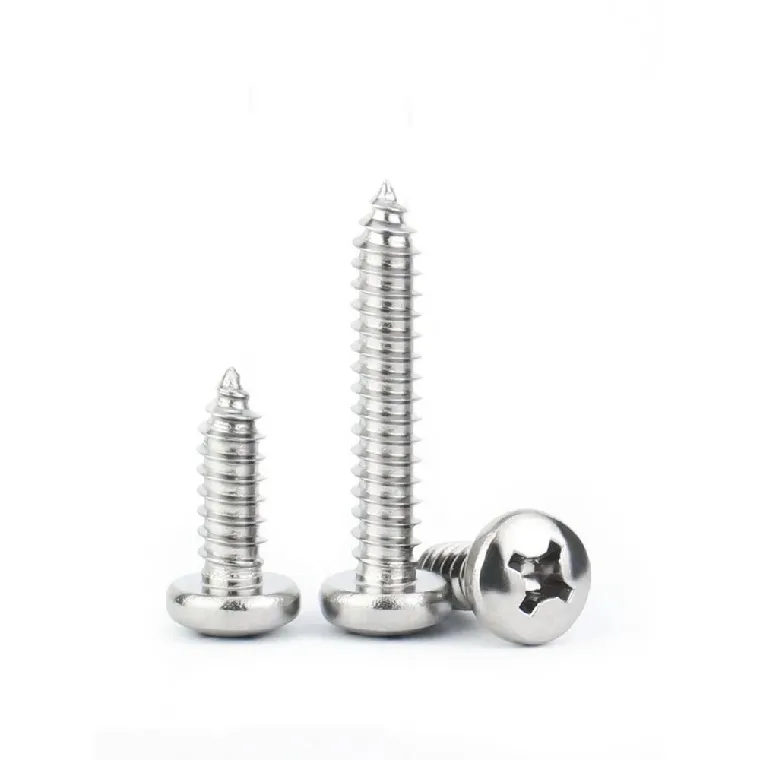
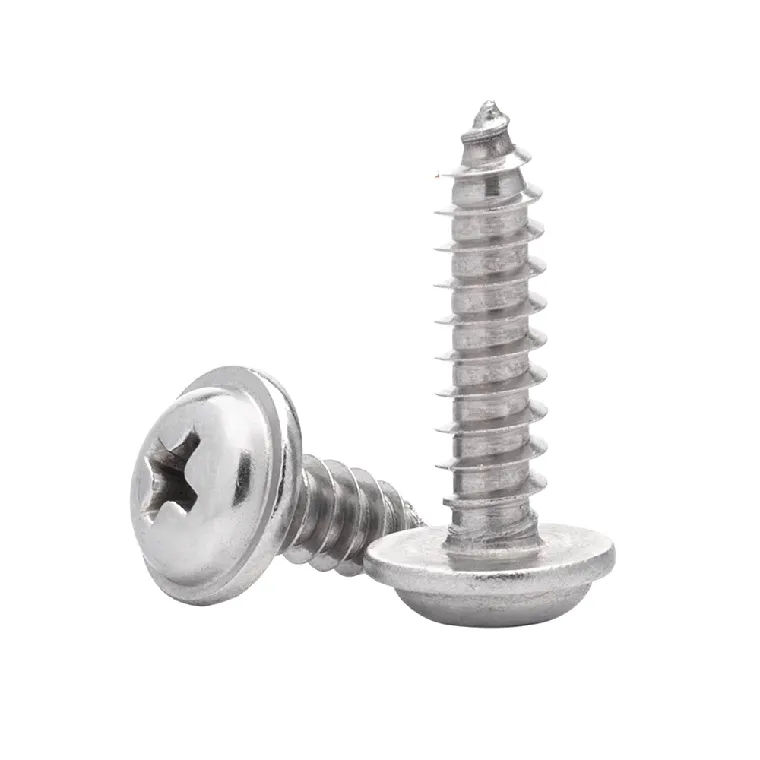
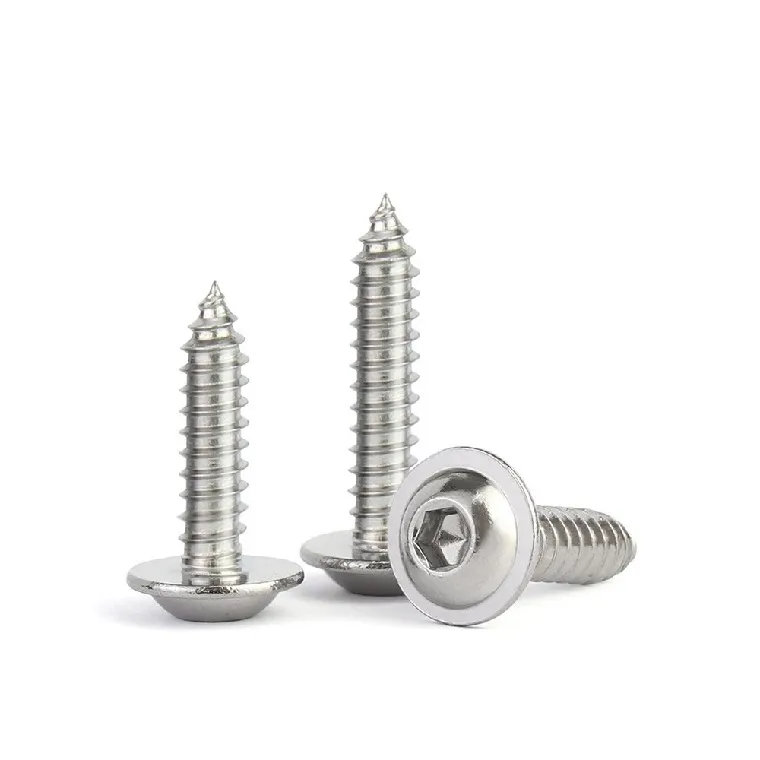
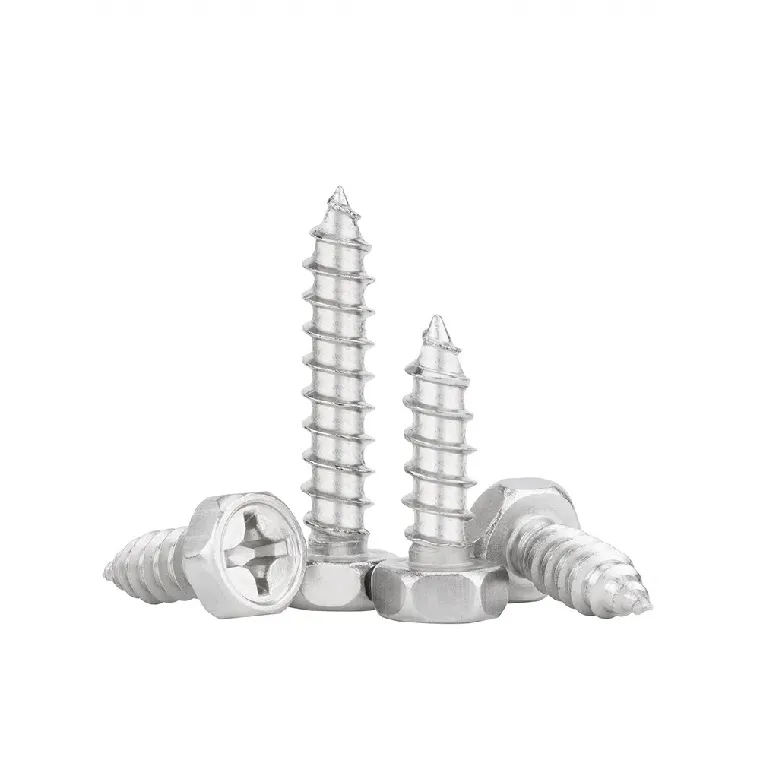
Stainless Steel Self Tapping Screws
Stainless steel self tapping screws are a common type of general fastener used for joining and securing various materials, especially wood panels, sheet metal, and plastics.
- Production Standard: DIN7981, DIN 968, DIN 7982, ISO14586
- Grade or Material: 18-8, A2 (304), A4 (316), SS 410
- Available Size: ST2.9, ST3.5, ST4.2, ST4.8, ST5.5, ST6.3
- Thread Length: Max 100MM
- Surface Treatment: Cleaning, Passivation
A2 A4 Stainless Steel Self Tapping Screws
A2 A4 Stainless steel self tapping screws are made primarily of stainless steel, a material that has excellent corrosion resistance and can remain stable in a variety of harsh environments.
These screws are characterized by their unique self-tapping ability to screw directly into materials without pre-punched holes, greatly simplifying the installation process.
304, 316 stainless steel is also very strong, making these screws able to withstand a great deal of tension, making them ideal for use in places that require high-strength connections.
In terms of construction, stainless steel self tapping screws usually have a flat or rounded head and a pointed tail to make it easier to screw into the material.
Additionally, the threads of self-tapping screws are designed in a very specific way; they are usually sharp to cut through the material and form new threads to hold firmly in place.
Stainless steel self tapping screws are widely used in a variety of industries, including automotive, construction, machinery, and electrical appliances.
Used in the automotive industry, they are used to connect various parts of the body; in the construction industry, they are used to fix various equipment and components; and in the machinery and electrical appliance industry, they are used to assemble various equipment and machines.
Types of Stainless Steel Self Tapping Screws
Good shape of the head and tail of stainless steel self tapping screws can vary according to specific needs and application scenarios.
Generally speaking, the head shape of stainless self-tapping screws mainly has round head, flat head, semi-countersunk head and countersunk head.
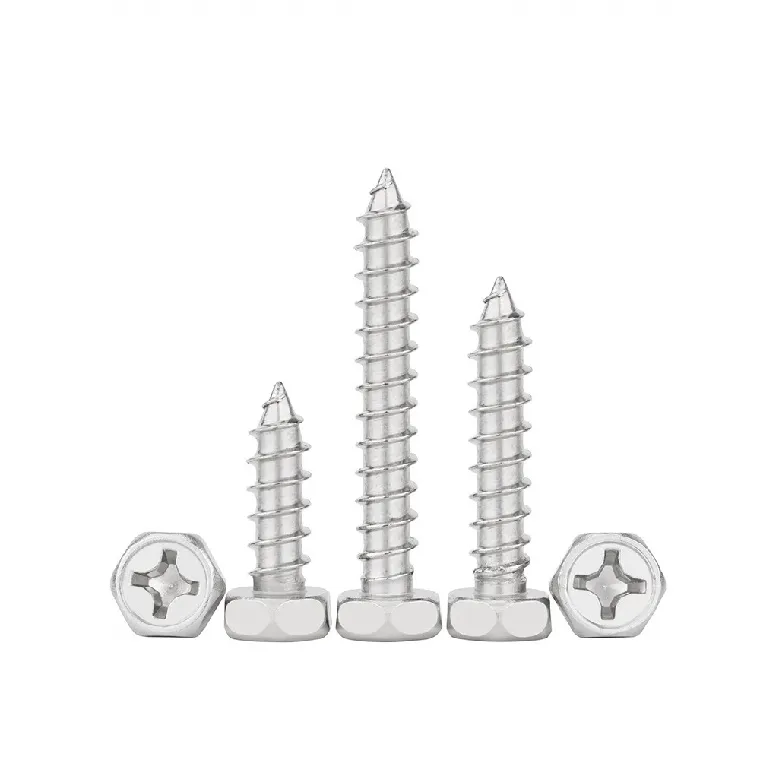
Flat Head Self-tapping Screws
Flat head self-tapping screws, can be connected with the surface of the better fit, applicable to some need for higher connection strength occasions
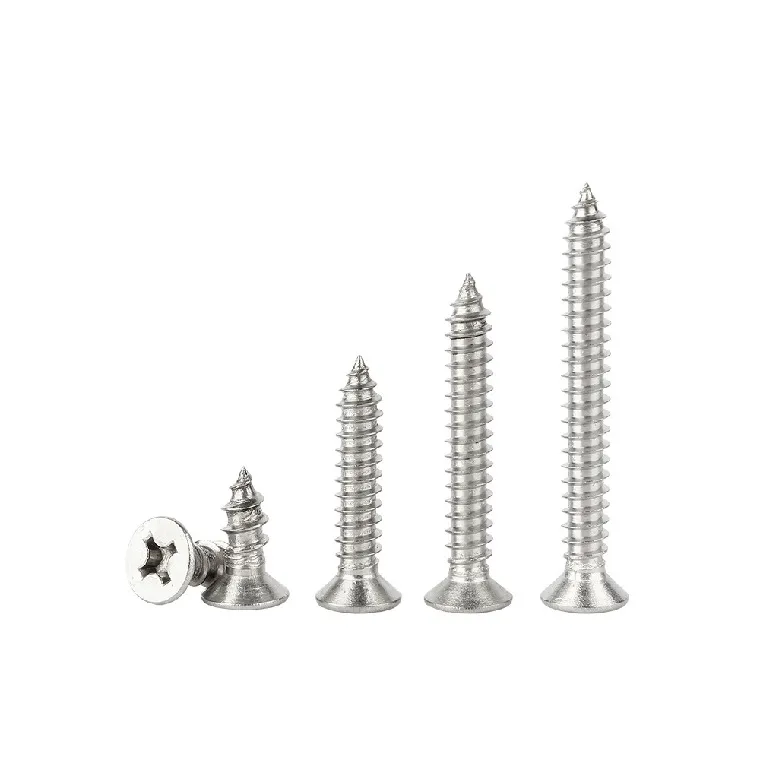
Countersunk Head Self-tapping Screws
Countersunk head self-tapping screws is between the round head and flat head, with a certain degree of decorative and connecting strength, applicable to some of the medium requirements of the occasion.
A2 or A4 stainless steel self tapping screws, on the other hand, usually have a pointed tail, which is designed to make it easier to screw into the material and form new threads.
A screw-pointed tail design reduces resistance when screwing in, improves self-tapping performance, and makes it easier for the screw to get inside the material.
In addition, the tail may be designed with different slots or thread shapes to accommodate different materials and installation needs.
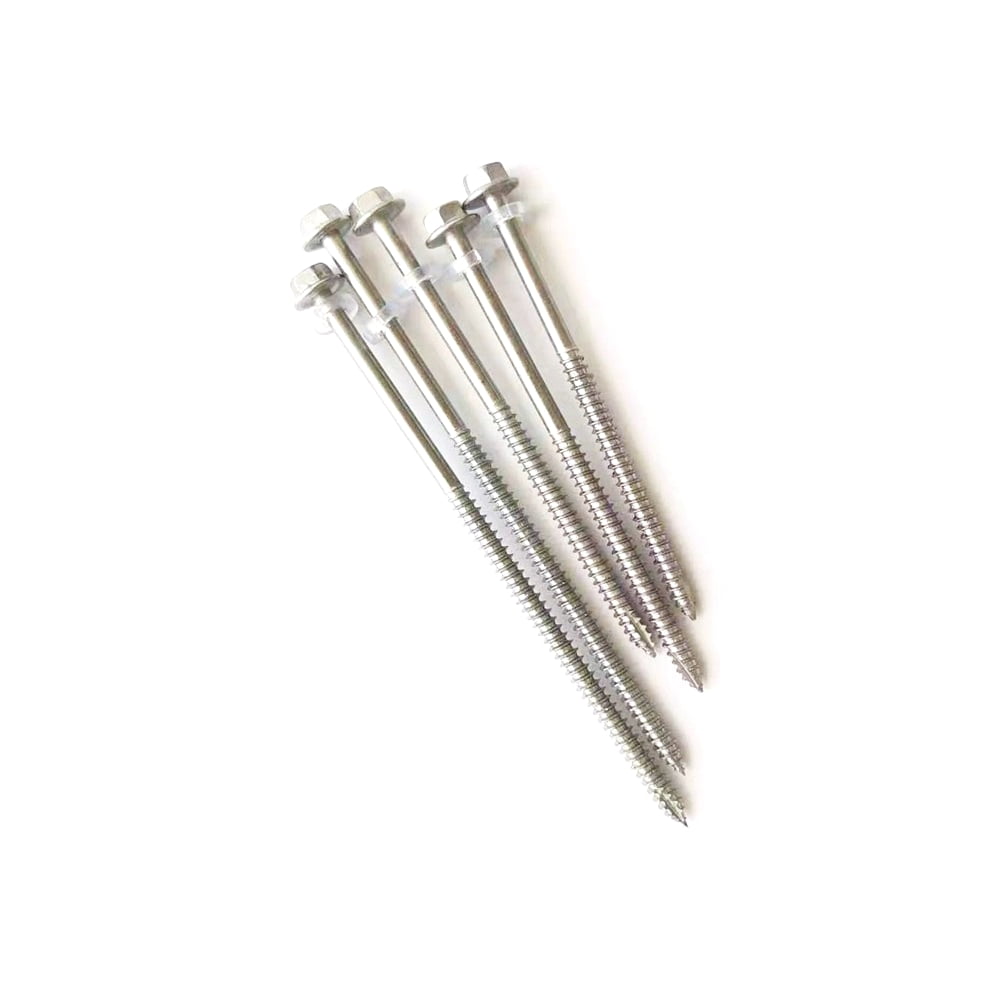
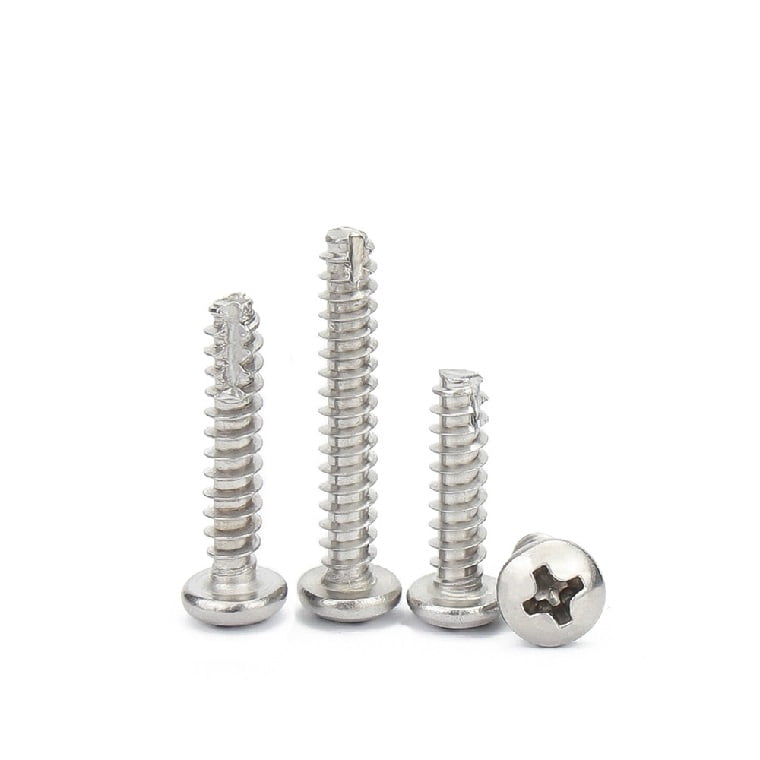
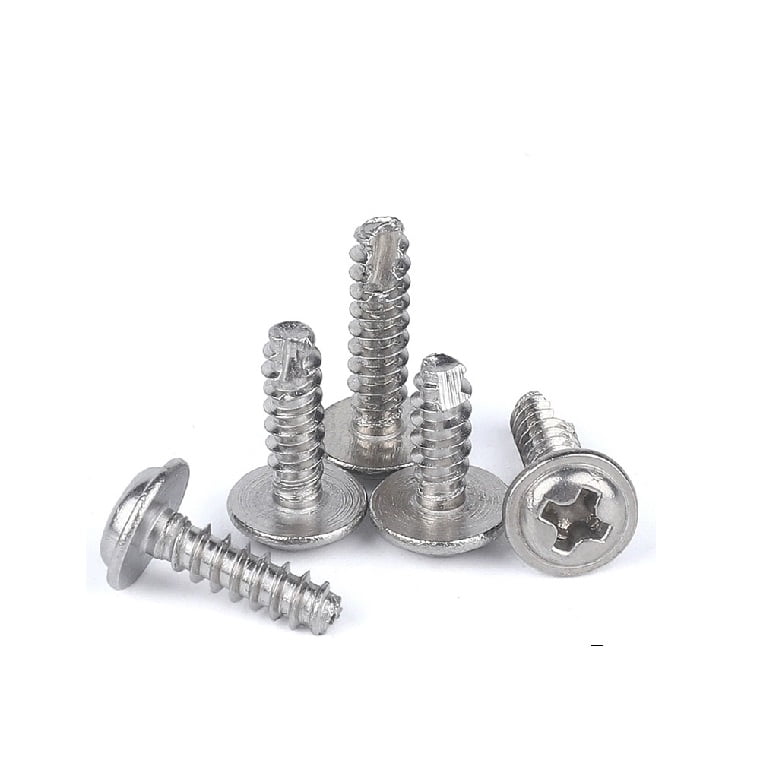
That head and tail shapes of stainless steel self tapping screws should be selected according to the actual use requirements to ensure that they can meet the expected performance and requirements.
At the same time, in the production and processing process, it is also necessary to strictly control the size and precision to ensure the quality and reliability of the self-tapping screws.
DIN 7981 Self Tapping Screw Sizes Chart
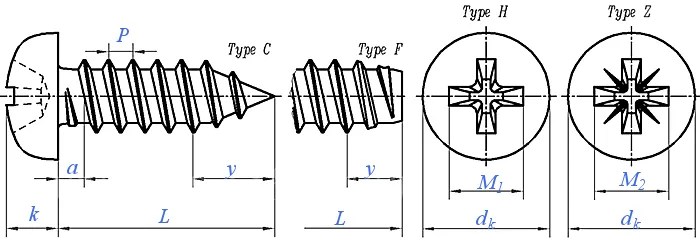
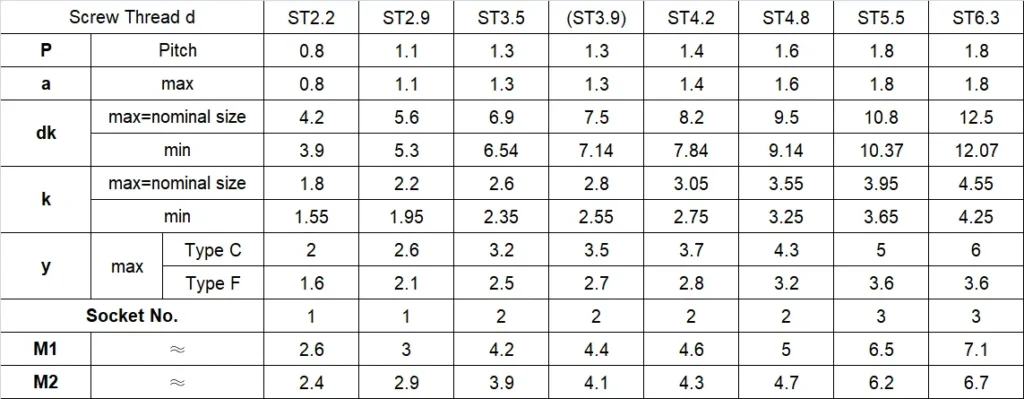
DIN 7982 Self Tapping Screw Sizes Chart
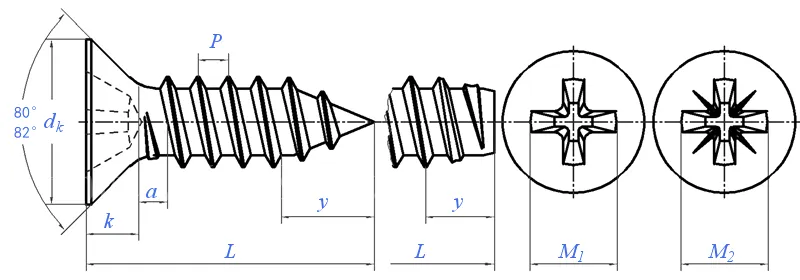
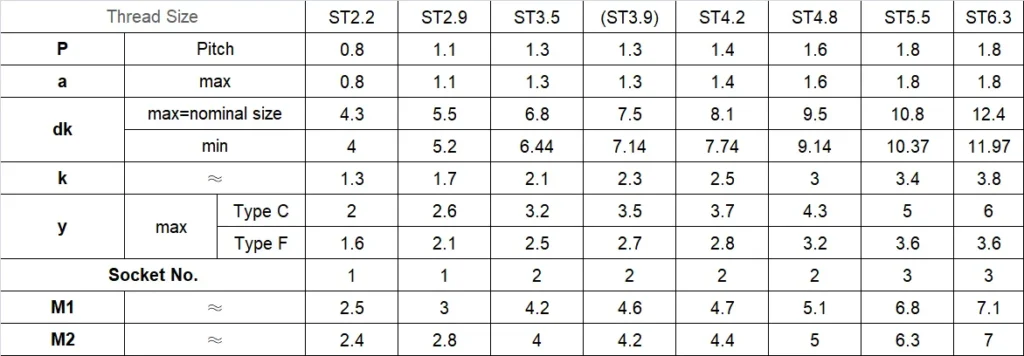
DIN 968 Self Tapping Screw Sizes Chart
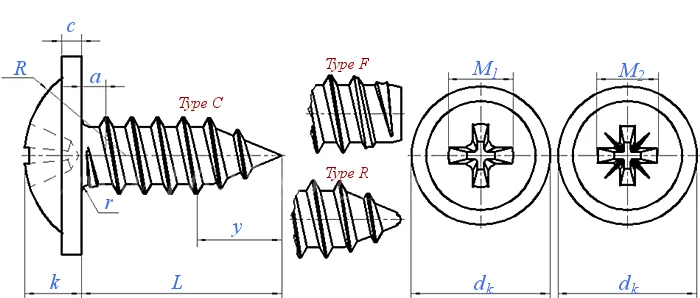

ISO 14586 Self Tapping Screw Sizes Chart
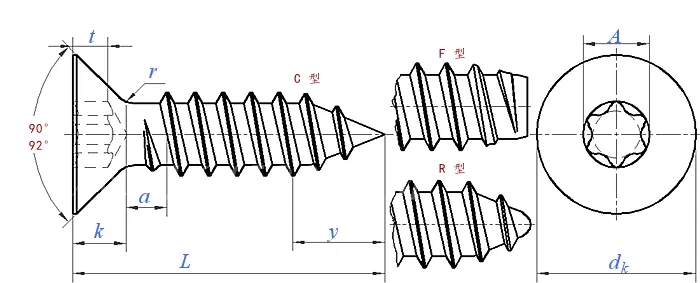

Material Of Stainless Steel Self Tapping Screws
Tapping screws are mainly made of austenitic 302, 304, 316, and “low nickel” 201.
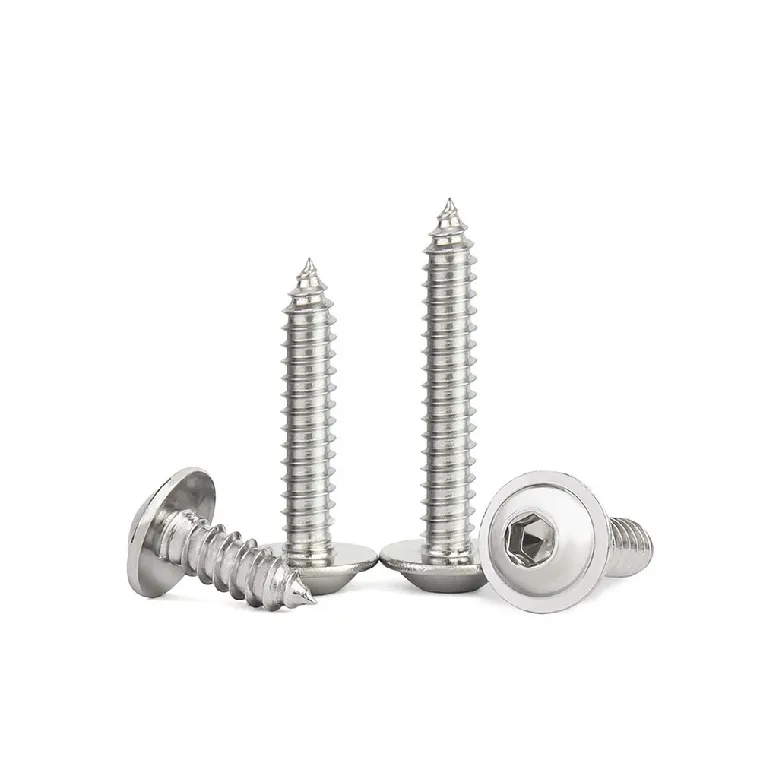
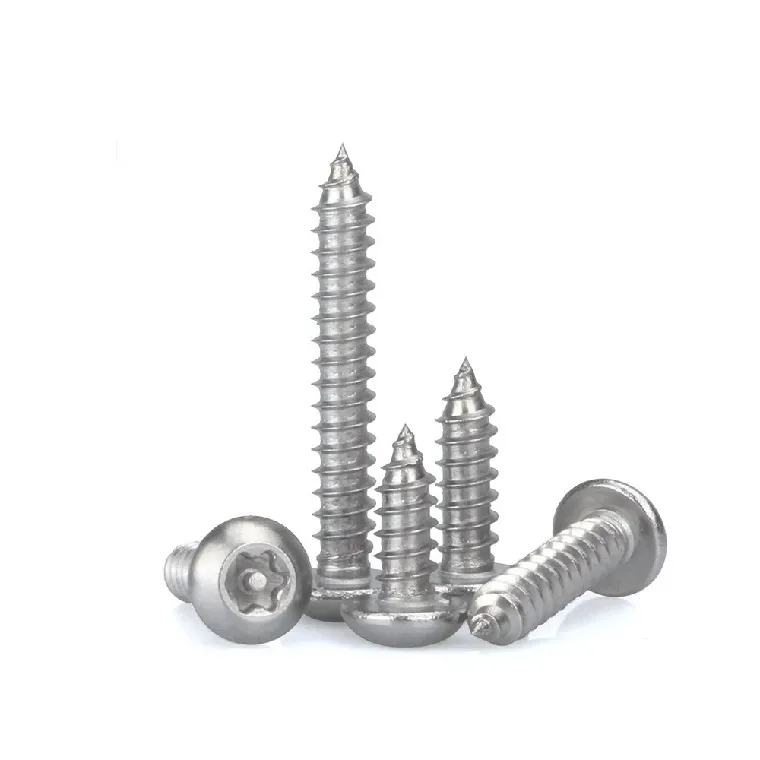
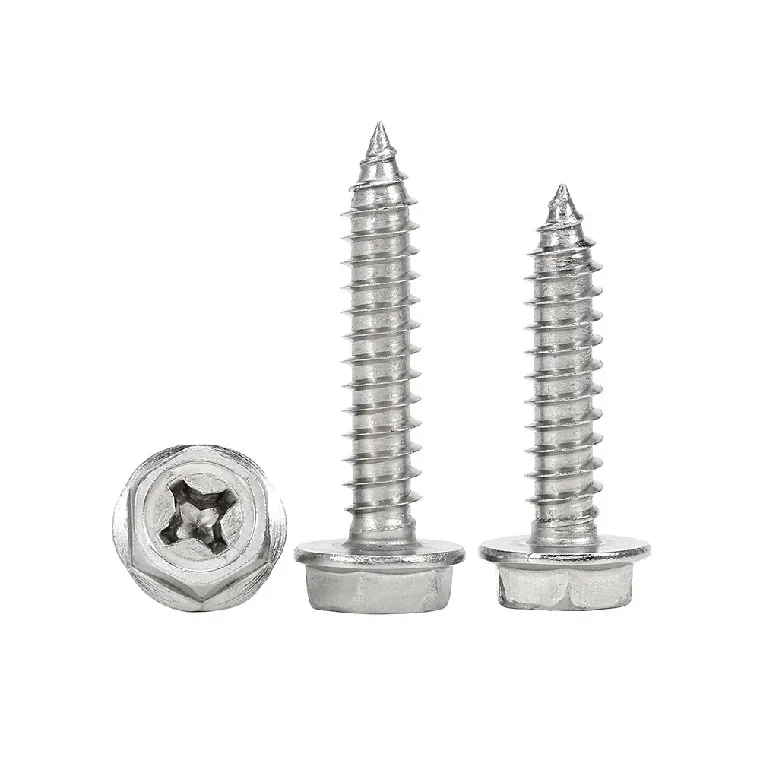
Among them, 304 stainless steel is the most commonly used material, it has excellent corrosion resistance, heat resistance, low-temperature strength, and mechanical properties, suitable for a variety of environments and use of the scene.
The material of stainless steel self-tapping screws should also have good self-tapping performance and cutting performance so that new threads can be formed and firmly fixed when screwing into the material.
It should be noted that different stainless steel materials have different characteristics and scope of application, so the selection of stainless steel self-tapping screws should be based on the actual use of demand to ensure that it can meet the expected performance and requirements.
Stainless Steel Self Tapping Screws Corrosion and Heat Resistance
430 304 316 material of stainless steel self tapping screws has a direct impact on its corrosion resistance and heat resistance.
First of all, the corrosion resistance of stainless steel is closely related to its material composition. Stainless steel contains chromium, chromium can be combined with oxygen to form a layer of dense oxide film, this film can prevent oxygen from further contact with the metal, thus playing a role in corrosion prevention.
316 and 316L stainless steel relative to 304 stainless steel contains higher nickel and molybdenum elements, which makes them in the face of some specific corrosive environments have better corrosion resistance.
Secondly, the heat resistance of stainless steel self-tapping screws is also related to its material. The heat resistance of stainless steel mainly depends on the type of its material and the content of alloying elements.
Austenitic stainless steel and duplex stainless steel have better heat resistance at high temperatures, while ferritic stainless steel has relatively poor heat resistance.
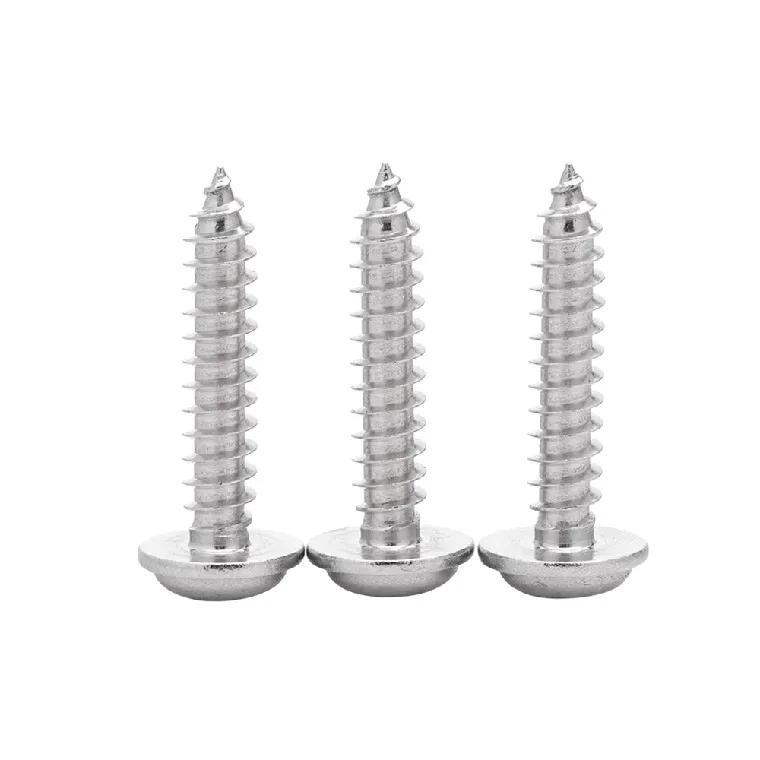
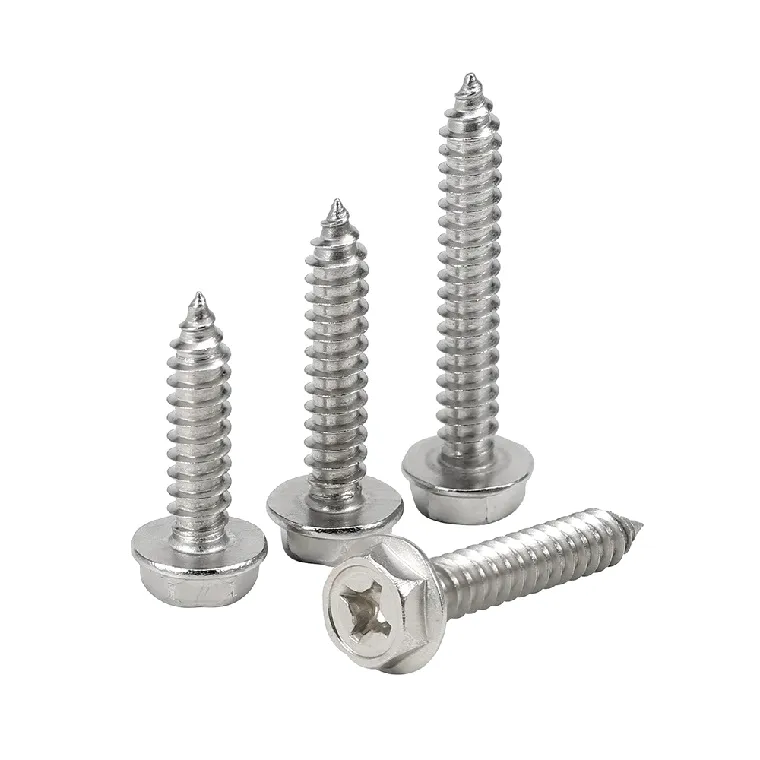
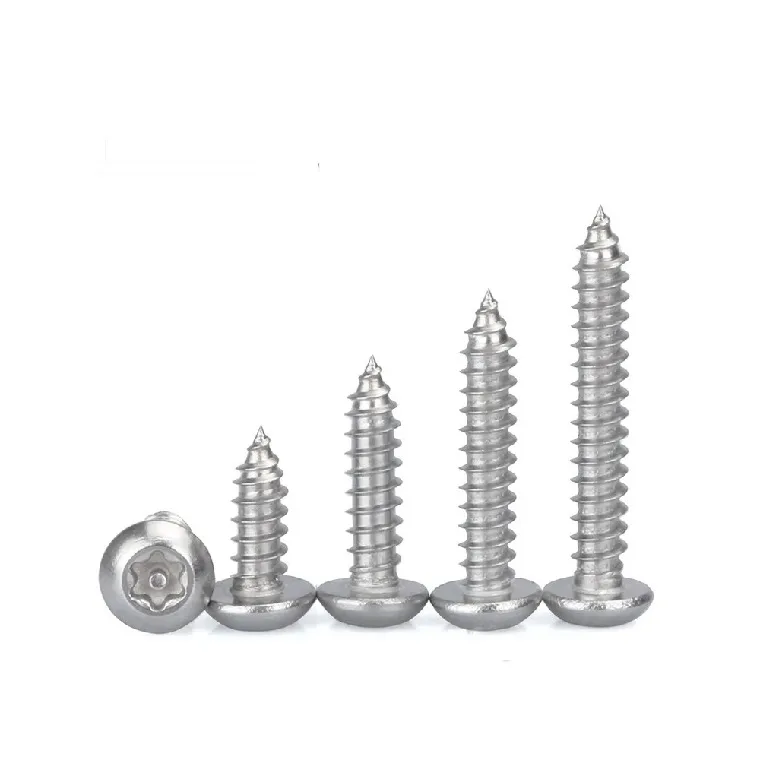
As stainless steel self tapping screws, the maximum working temperature of 316L stainless steel can reach 815℃, while the maximum working temperature of 18-8 stainless steel is 650℃.
Screw surface treatment of stainless steel self-tapping screws also affects their corrosion resistance and heat resistance.
Nickel plating can improve the corrosion resistance of screws, but oxidation reactions and corrosion may occur at high temperatures and in acidic and alkaline environments. Chrome plating has better corrosion resistance in dry environments, but may be susceptible to corrosion in wet environments.
Therefore, when choosing stainless steel self tapping screws, it is necessary to choose the appropriate material and surface treatment process according to the specific use environment and requirements, in order to ensure that it has good corrosion resistance and heat resistance, so as to ensure the stability and safety of the equipment
Surface Ttreatment of Stainless Steel Self Tapping Screws
SS self-tapping screws surface treatment is an important step to improve product quality, increase aesthetics and improve corrosion resistance. The following are common surface treatment methods for stainless steel self-tapping screws:
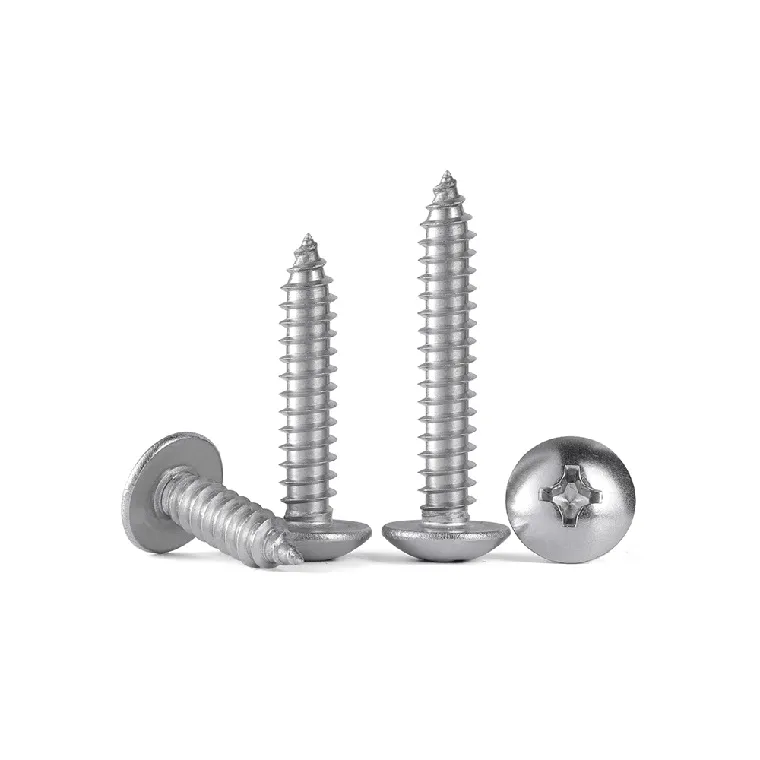
Cleaning and Degreasing
Cleaning and degreasing is the first step in surface preparation and is designed to remove oil, dirt and other impurities from the surface of the screw. This usually involves soaking, brushing or spraying the screws with a cleaning agent or solvent, followed by thorough rinsing and drying.
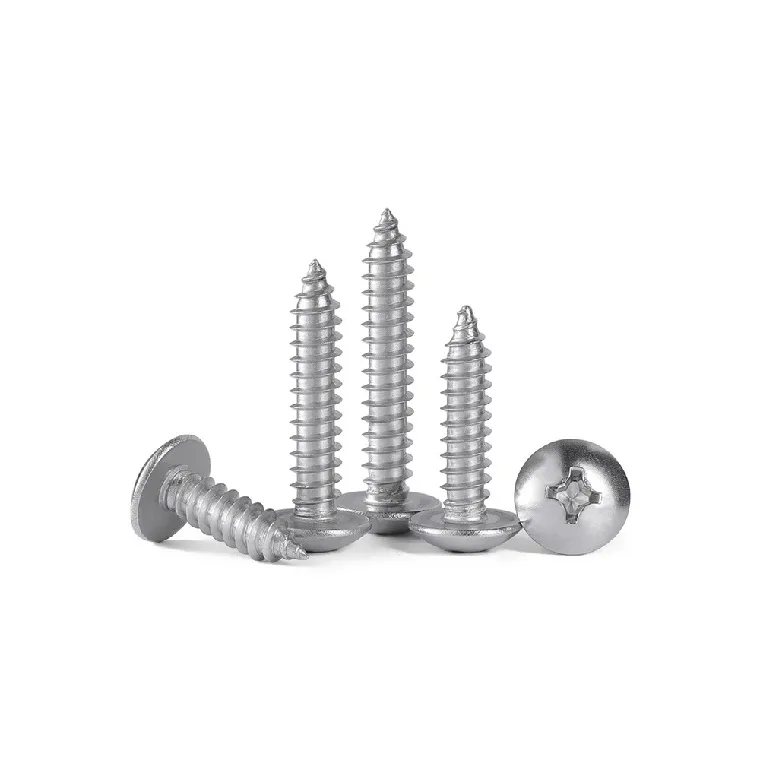
Mechanical Polishing
Mechanical polishing involves the use of mechanical force to remove rough portions of a surface in order to achieve a smooth surface. This is usually done using tools such as polishing machines, grinding wheels or abrasive belts. The polished surface of screws is smoother and can improve their corrosion resistance.
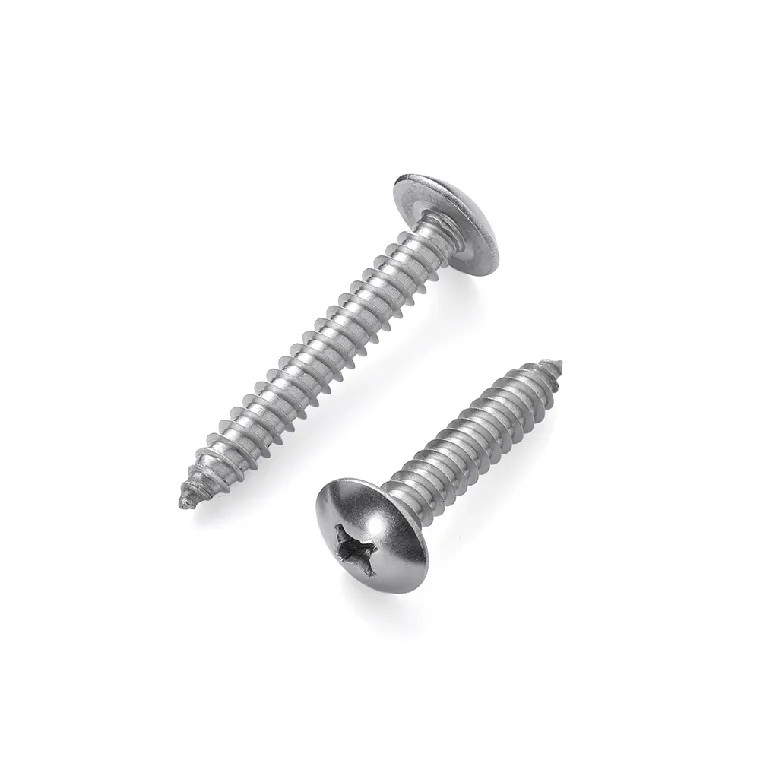
Electroplating
Electroplating treatment is the deposition of a layer of metal or alloy on the surface of a screw to increase its aesthetic appeal, corrosion resistance or electrical conductivity. Common plating treatments include nickel plating and so on.
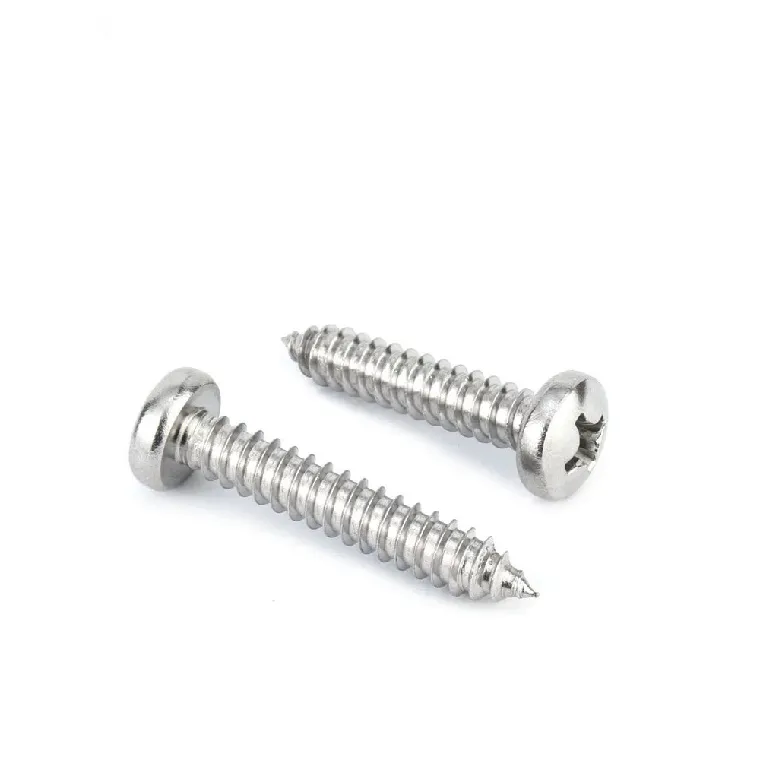
Electrophoretic Coating
Electrophoretic coating is a special coating method in which the coating is uniformly applied to the surface of the screws by means of electrophoresis. This method results in a uniform, smooth coating with a strong bond between the coating and the substrate.
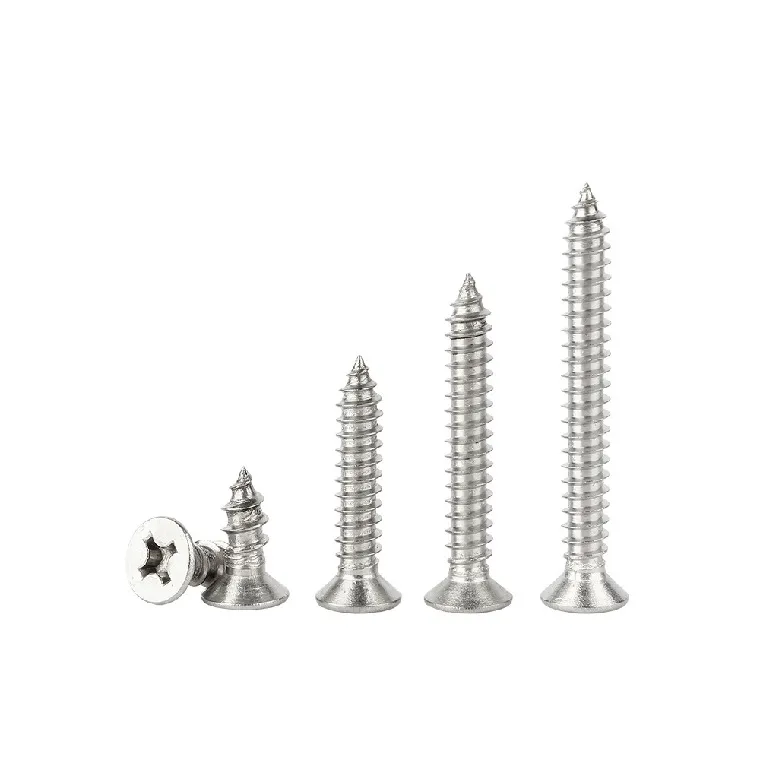
Anodizing
Anodizing is a special surface treatment process used primarily for aluminum and aluminum alloys. Although stainless steel is not often anodized, an oxide film can be formed on the surface of stainless steel by a similar method to increase its corrosion resistance and decorative qualities under certain specific circumstances.
Overall, stainless steel self tapping screws are a very practical fastener with excellent corrosion resistance and high strength, which can be easily installed and fixed in a variety of materials and occasions.
With the development of industry and application requirements, the design and performance of stainless steel self-tapping screws will continue to improve and perfect!
Free Sample Stainless Steel Self Tapping Screws
304, 316 and 410 Self Tapping Screw samples are free from us, we can supply 10 pcs of each length for your testing, before sending by courier, EN10204 MTC is available.
Do you want to check our rate for ss self drilling screw, Please send your full enquire, we will reply you within 24 hours.